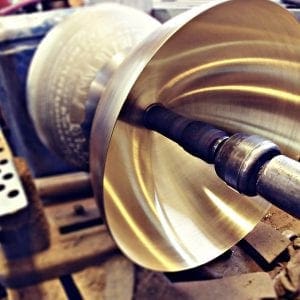
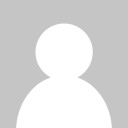
Metal Spinning Advantages and Disadvantages
This blog post aims to address these questions, the first in brief, the second in a little more detail by highlighting the advantages and then the disadvantages.
Share this article:
What do you most commonly associate with the word ‘continuous’? Ceaseless, continual, eternal, everlasting, constant, incessant are synonyms that may spring to mind.
For fellow craftsman, the continuous cycle of machinery and the noise pollution associated with it may not be the best approach when manufacturing products.
In this case, it may be best to explore different processes that are better suited for your manufacturing company. We have you covered here with our guide to The Six Types of Manufacturing Process.
If, on the other hand, you are here to delve deeper into the world of Continuous Manufacturing, keep on reading!
Continuous Manufacturing is often known as Process Manufacturing (Continuous) and operates with the use of production lines that run 24/7. Unlike processes such as Repetitive, Discrete or Job Shop Manufacturing, raw materials used within this process consist of gases, liquids, powders or even slurries.
The purpose of continuous manufacturing is to produce, manufacture or process materials uninterrupted. Continuous manufacturing gets its name because materials are constantly being processed, during which they experience chemical reactions or some form of heat treatment.
It differentiates itself with that of process manufacturing (Batch) which we will explore in greater detail in a future blog. In comparison, the entire process within Process manufacturing (continuous) goes through one movement in one location and is monitored throughout production to identify key areas of improvement within the process. Process manufacturing (Batch) on the other hand, consists of different stages of production being handled in different areas or companies.
To simplify this process, let’s take a material used within continuous manufacturing and add it to point A. The finished product is produced, and leaves point B. In between point A and B, there may be other areas the product leaves (Point C) as the same material in use can produce other products.
If you had oil refineries in mind when thinking about a product within this process, you would be correct. Other companies that use this process include those within the smelting industry as well as power stations, wastewater treatment and more.
Let us take a closer look at an example.
As a Metal Spinning business, we work with various forms of Steel such as 304 Stainless Steel, so in this example we will explore how a steel manufacturing plant would use continuous manufacturing.
The aim of continuous manufacturing is to create large volumes of standardised products, in this case millions of tonnes of steel per year.
At point A, liquid steel would be processed for casting whilst at point B, thin sheets of steel would be rolled out and shipped to their designated destinations. In between point A and B, the steel will undergo different levels of treatment with the use of machinery. This flow production will be uninterrupted and with everything occurring at the same time.
Check out this video to see continuous manufacturing in action within a steel manufacturing plant.
Continuous production is somewhat different to continuous manufacturing because it includes assembly lines that manufacture products with sub-assemblies. This is a manufacturing technique that you would be familiar with having read our guides on Repetitive Manufacturing or Discrete Manufacturing. There are two types of continuous production that manufacturers worldwide are using within continuous manufacturing. They include;
Mass Production:
The manufacture of large quantities of standardised products. The key characteristics of continuous manufacturing are ever present in the form of an uninterrupted flow, the process, the materials and the machines in operation
Process Production:
The demand for products within process production are continuous and high. The materials also produce different products at different stages of the manufacturing process. Take the aforementioned oil refinery that would produce diesel, petrol and jet fuel for example.
The production workflow can also be categorised into the following;
In this section we will explore the advantages and disadvantages of adopting continuous manufacturing within your workplace. As with all processes, they are ever present and it’s important to understand first, if this process is suitable for your business model and secondly, whether you can mitigate the risks and reap the rewards.
The Advantages:
The Disadvantages:
Is Continuous Manufacturing processes something your business has adopted? What are your thoughts on this manufacturing process? Don’t forget to share this page on social media and tell us your thoughts on the topic!
This blog post aims to address these questions, the first in brief, the second in a little more detail by highlighting the advantages and then the disadvantages.
Share on facebook Share on twitter Share on linkedin Share on pinterest Machinery Expansion Excell Metal Spinning Ltd. expands with new Machinery upon investments worth
Share on facebook Share on twitter Share on linkedin Share on pinterest Holiday Season Metal spinning tools will be downed, and turkey’s will be prepped.
Units 9 & 10 Gunners Building, Limberline Road, Hilsea
Portsmouth, PO3 5BJ
(+44) 02392-666456
Sales@excellmetalspinning.com